Auxiliary Additives for UV Light Curing Coatings
Introduction:
In the field of coatings, the power of UV light curing technology has revolutionised efficiency and quality. Auxiliary additives are additives used to perfect certain properties of coatings during the manufacturing, construction application and transport and storage of light-curing coatings, usually photoinitiators, defoamers, levelling agents, wetting and dispersing agents, matting agents, and so on. In this article, we will look at the role and impact of additives specifically tailored for UV-curable coatings.
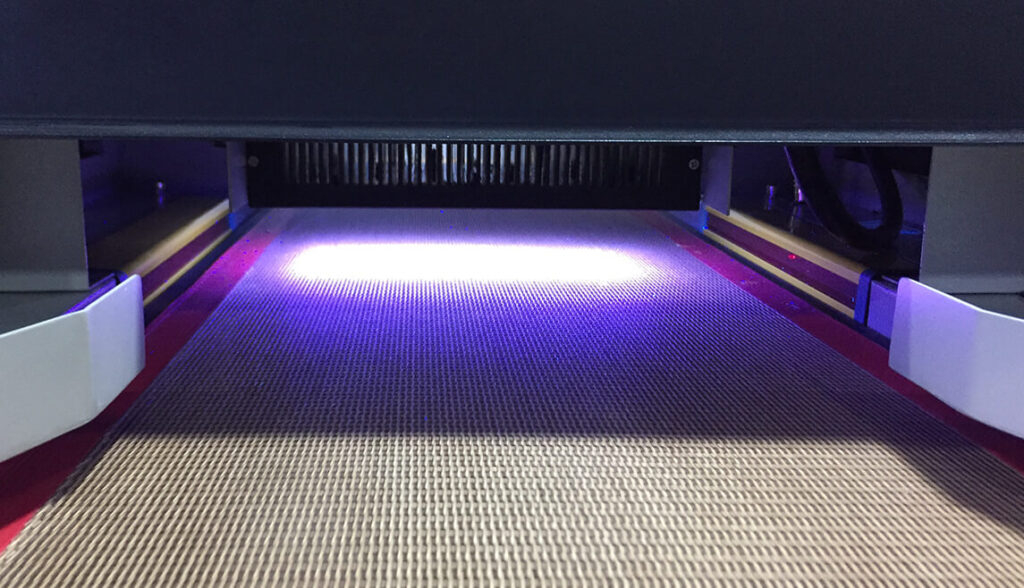
Photoinitiators: Catalysts for Curing
UV light-curing coatings utilise the power of light to initiate a polymerisation reaction for rapid curing. Photoinitiators are the heroes of the process, absorbing UV light and triggering the conversion of the liquid coating to a solid film. These additives result in a rapid and uniform cure, resulting in coatings that are not only tough, but also more chemically resistant.
Levelling properties:
BZ-603 acrylate levelling agent can reduce the surface tension of light-curing coatings in the process of making, and solve the problems caused by the rise of coating viscosity. By reducing surface tension, this additive allows coatings to cover intricate details and complex geometries with excellent consistency.
Wetting and dispersing agent:
Achieving stable dispersion is a challenge in any coating process, and both BZ-4010 and BZ-2209 wetting and dispersing additives improve alignment and milling time of UV-curable coatings, ensure pigment stability, and add gloss to coatings.
Anti-settling:
UV cured coatings often contain pigments or additives that may settle over time, BZ-4010 wetting and dispersing additive prevents this problem by maintaining a stable suspension of particles in the coating formulation. This ensures that the final cured coating retains its intended properties without any undesirable changes.
Antifoams:
UV curable coatings can be configured to produce air bubbles that can seriously affect the performance of the coating. The use of BZ-4920 defoamer eliminates the bubbles that occur when the coating is manufactured and stirred for application. The defoamer is suitable for various systems, and has good recoatability and does not contain silicone.
Matting Agents:
Matting agents affect the final appearance of UV-curable coatings by controlling their gloss level. By adding matting agents, manufacturers can achieve a variety of appearances, from high-gloss to satin or matte, to tailor the aesthetics of the coating to the specific application.
In Summary:
UV-cured coatings are transforming industries, offering unprecedented efficiency and performance. The key to their success is carefully selected additives that enhance levelling properties, wetting properties, appearance and protection. These additives, in combination with others, make coatings superior to traditional alternatives, giving your coatings a strong competitive edge in the marketplace.
At [Camen Chemical], we specialise in formulating UV curable coating additives to enhance the potential of coatings. Contact us to learn how our additives can bring efficiency, toughness, and brilliance to your coating process.
People who read this article also read the following articles:
Additives to Enhance the Performance of Printed Circuit Board Inks